product
Solar Cell Grade Silicon Wafer
Solar cell-grade silicon wafers are the fundamental building blocks of photovoltaic (PV) technology, enabling the efficient conversion of sunlight into electricity. These wafers are manufactured from high-purity silicon, typically using the Czochralski or Float-Zone process, ensuring minimal impurities for optimal electrical performance. Depending on the application, solar wafers are categorized into monocrystalline and polycrystalline types, with monocrystalline wafers offering higher efficiency due to their uniform crystal structure. Advanced surface treatments, such as texturing and anti-reflective coatings, enhance light absorption and improve energy conversion rates. As solar energy continues to be a key driver of sustainable power generation, innovations in wafer technology, including thinner designs and higher purity materials, are pushing the boundaries of efficiency and cost-effectiveness in the renewable energy sector.
Manufacturing Process
- Silicon Ingot Growth – Purified silicon is melted and formed into ingots.
- Wafer Cutting – Ingots are sliced into thin wafers.
- Doping & Etching – The wafer is treated to improve electrical conductivity.
Microchips (Semiconductor Chips)
Microchip-grade silicon wafers are at the heart of modern semiconductor technology, serving as the essential foundation for microprocessors, memory chips, and advanced computing devices. These ultra-pure, monocrystalline wafers undergo precision engineering to meet the stringent requirements of next-generation electronics, including AI-driven processors, quantum computing, and 5G communication systems. As semiconductor manufacturing evolves, innovations in wafer technology, such as smaller node sizes, enhanced doping techniques, and defect-free surfaces, are driving unprecedented performance gains. With the increasing demand for high-speed, energy-efficient chips, microchip-grade silicon wafers continue to redefine the future of computing, enabling breakthroughs in artificial intelligence, IoT, and smart devices.
Manufacturing Process
- Final Quality Control: Verifying performance before distribution.
- Silicon Ingot Growth: Pure silicon is melted and formed into cylindrical ingots.
- Testing & Inspection: Chips are tested for defects and performance.
How silicon waffer are made
A wafer is a slice of silicon roughly 1 millimeter thick that has an extremely flat surface thanks to procedures that are technically very demanding. The subsequent use determines which crystal growing procedure should be employed. In the Czochralski process, for example, the polycrystalline silicon is melted and a pencil-thin seed crystal is dipped into the molten silicon. The seed crystal is then rotated and slowly pulled upwards. A very heavy colossus, a monocrystal, results. It is possible to select the monocrystal’s electrical characteristics by adding small units of high-purity dopants. The crystals are doped in accordance with the customer specifications and then polished and cut into slices. After various additional production steps, the customer receives its specified wafers in special packaging, which allows the customer to use the wafer immediately in its production line.
Czochralski process
Czochralski Process
Today, a large portion of the silicon monocrystals are grown according to the Czochralski process,which involves melting polycrystalline high-purity silicon in a hyperpure quartz crucible and adding the dopant (usually B, P, As, Sb). A thin, monocrystalline seed crystal is dipped into the molten silicon. A large CZ crystal then develops from this thin crystal. Precise regulation of the molten
silicon temperature and flow, the crystal and crucible rotation, as well as the crystal pulling speed results in an extremely high-quality monocrystalline silicon ingot.
Cylindrical Grinding
Cylindrical Grinding
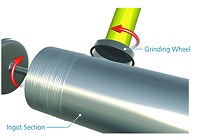
After segmenting and comprehensive quality control, the onocrystalline CZ or FZ silicon pieces are prepared for the wafering process. This means first precisely aligning the crystals, then cylindrical grinding of the ingot pieces to the required diameter. The final step is grinding orientation markings, such as notches for large-diameter wafers or straight edges (flats) on the side of small wafers.
Wire Slicing
Wire Slicing
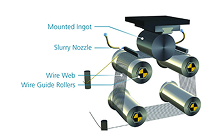
The first step when wafering the silicon ingots is multi-wire slicing, which is the slicing method commonly employed today. A very thin metal wire, which can be many miles long, is pulled over the wire guide rollers in such a way that a wire web with very precise spacing is spanned. Nozzles apply the slurry to the web while the silicon ingot is slowly pushed through the web. This technology makes it possible to slice complete silicon ingots into hundreds of silicon wafers in just one step. The individual process parameters must be carefully monitored in order to guarantee that the wafers are uniformly thick and that the two faces of each wafer are parallel to each another.
Edge Rounding
Edge Rounding
Monocrystalline silicon is a very brittle material with a high risk of breaking. Special care is consequently needed in order to avoid mechanical damages on the edge of the wafer.
The unrounded silicon wafer is mounted onto a grinding chuck and a profile rounding wheel rounds the edge of the wafer. The edge profile is rounded to match the customer specifications. Each wafer is optimized in order to avoid processing damages and maximize the yields in the component processes, such as CMP and lithography.
Laser marking
Laser marking
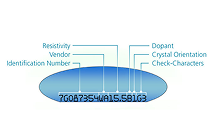
Laser marking is used to identify individual wafers or wafer batches in order to allow manufacturing traceability. Laser marking can take place in accordance with either industry standard or customer specifications. As a rule, the markings contain information on the wafer supplier, some technical information, and an individual wafer number.
Lapping
Lapping
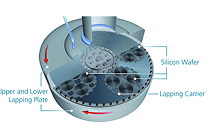
After the wafers have been sliced and the edges have been rounded, the wafers are lapped (or alternatively ground) in order to increase the parallelism of the silicon wafer surfaces and to remove any damage below the surface caused by the slicing process. For lapping, the silicon wafers are held in carrier wheels (lapping carriers) between the upper and lower lapping plates, which rotate in opposite directions. The addition of an abrasive (lapping slurry) helps remove roughly ten micrometers of silicon from each wafer surface.
Cleaning And Etching
Cleaning And Etching
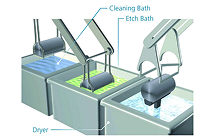
After the mechanical wafer processing, the silicon wafers are cleaned and etched in order to eliminate any remaining mechanical damage. Alkaline solutions, acids, or a combination of the two can be used for the etching.
Polishing
Polishing
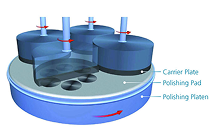
Polishing makes the silicon wafer surface smooth as glass and further improves the flatness. Wafers with a diameter of 200mm or less are usually polished on one side. The wafers are mounted on support plates and pressed against a polishing cloth that lies on a polishing plate. Wafers with a diameter of 300mm are polished on both sides. Like in the lapping process, the wafers are held by plates and simultaneously polished on the front and back by upper and lower polishing plates. The polishing agent (polishing slurry) and the pressure scheme determine the finished wafer’s surface quality and flatness.
Epitaxy
Epitaxy
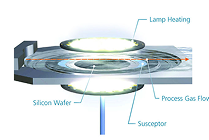
Applications with the toughest requirements call for silicon wafers with an especially high surface quality. In these cases, a thin, defect-free crystal layer is additionally deposited onto the polished surface from the gas phase. To apply the epitaxial layer, the silicon wafer is fastened to a susceptor and heated to a high temperature with the help of infrared lamps. The process gas flow and temperature are carefully controlled in order to create an epitaxial layer with a very homogeneous resistance and thickness profile.